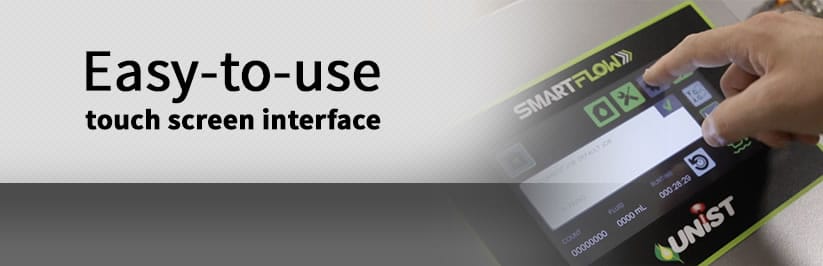
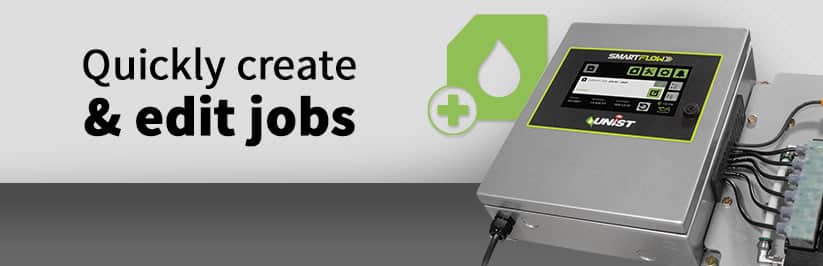
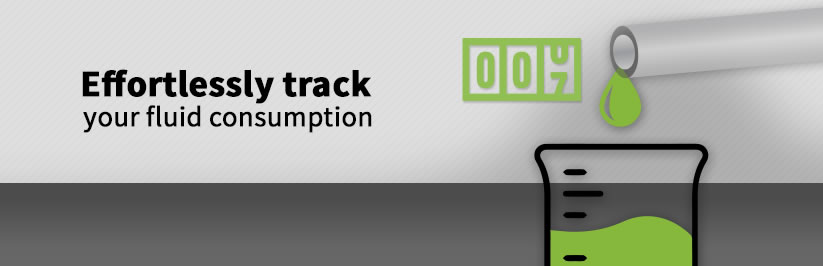
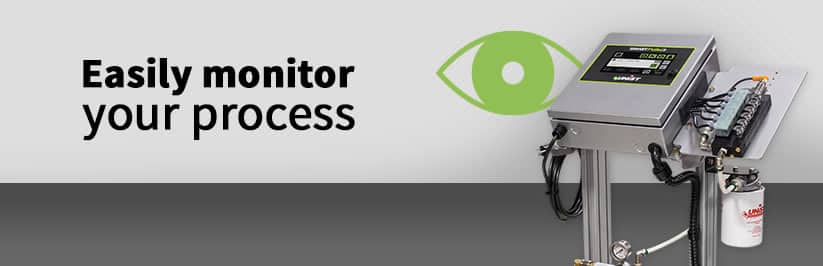
SmartFlow®
Product Info
Get smart with fluid application
The SmartFlow® allows metal formers to take full control of die and stock lubrication. This full-featured, programmable fluid controller makes configuring, controlling, monitoring, and tracking fluid application easier than ever, leading to increased profits from the stamping or forming operation.
Designed around an intuitive and easy-to-use operator interface, the SmartFlow® provides simple and guided setup, advanced press control integration, fluid usage tracking, process monitoring, and enhanced diagnostic and maintenance tools.
Save and recall jobs manually or utilize the press control interface for easy, automatic changeover. Back up and transfer jobs and settings between lines with a USB flash drive and the SmartFlow's® USB port. Pair the SmartFlow® controller with Unist's proven line of precision fluid applicators for an intelligent lubrication system that eliminates wasted fluid and mess, reduces scrap, and maximizes profits.
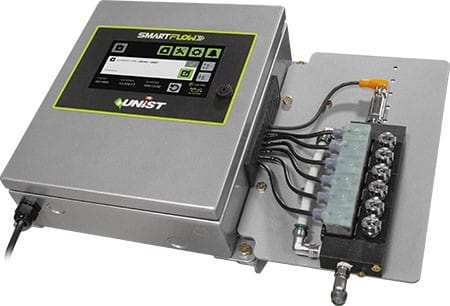
The automatic lubrication system intermittently actuates a bank of fluid Solenoid Valves (up to 22 outputs) that dispense a programmed quantity of fluid to specific lube points. The valve actuation on this electronic fluid dispenser is determined by production line rates so there is no under or over lubrication whether it is a stamping press or roll forming operation.
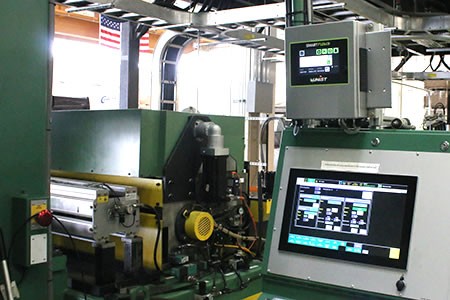
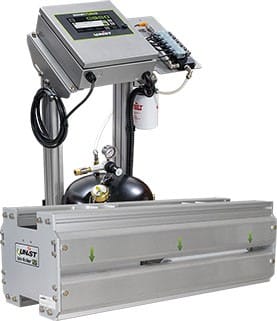
SmartFlow® Benefits
- Monitors critical parameters
- Precision fluid control
- Controls up to 22 outputs
- Stores up to 250 different setups/jobs
- Access code prevents tampering
- Saves fluid: precisely controls fluid
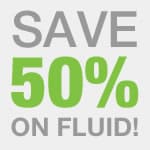
Combine the SmartFlow® with a Uni-Roller® applicator to reduce fluid usage and save money
On average, a Unist automatic lubrication system can reduce stamping fluid consumption by 50% with some customers reporting reductions as high as 90%!
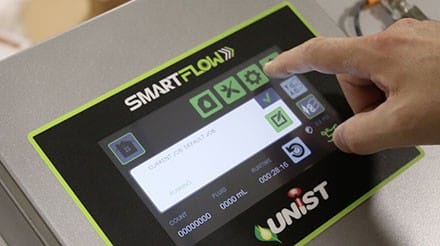
Touch screen interface
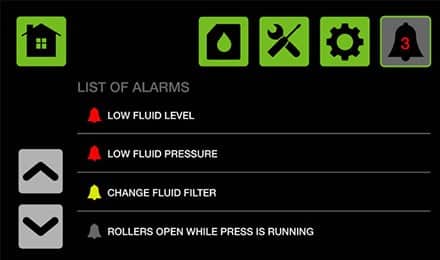
Process monitoring
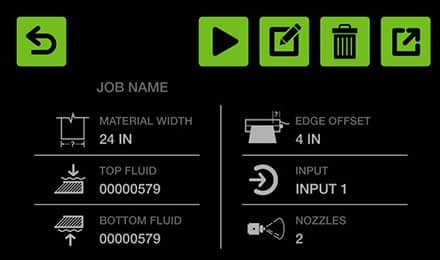
Easily create jobs
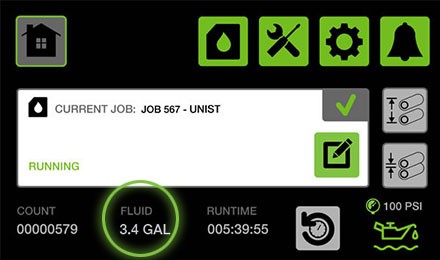
Fluid tracking
SmartFlow® Applications:
Provides programmable control for the following applications/Unist systems:
- Punching
(Mini-Roller™, Uni-Roller® S2) - Stamping
(Mini-Roller™, Uni-Roller® S2, Uni-Roller S2 Powered®, TSL™ System, Low Volume Spray Nozzle) - Fine blanking
(Uni-Roller® S2, Uni-Roller® S2 Powered)
- Deep Drawing
(Uni-Roller® S2, Uni-Roller® S2 Powered) - Application of rust preventives & protective coatings
(Low Volume Spray Nozzle, Uni-Roller® S2)
Delivers return on investment in less than 6 months
SmartFlow® controller and Uni-Roller® lubricator uses 50 to 90% less lubricant. Plus it decreases the mess, the parts cleaning, fluid recycling and costs associated with in-die spray systems, rag technology and externally lubricated rollers.
Features, Specs & Options
Features
- Touch screen interface
- Easy job creation
- Process monitoring (pressure, flow, valve performance, and line status)
- Fluid tracking - directly measure how much fluid your process is using!
Technical Specifications
|
|
|
|
Power supply: |
|
|
|
Cycle inputs: |
|
|
|
Maximum cycle input rate: |
|
|
|
Alarm inputs: |
|
|
|
Outputs: |
|
|
|
Alarm interlock relay: |
|
|
|
Operating temperature range: |
|
|
|
Storage temperature range: |
|
|
|
Press control interface: |
|
|
|
Job storage: |
|
|
|
Job transfer: |
|
|
Options & Accessories
Options & Accessoires
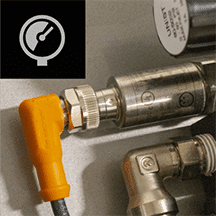
Pressure transducer
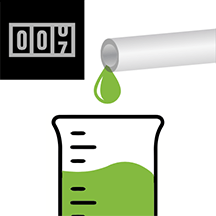
Flow totalizer
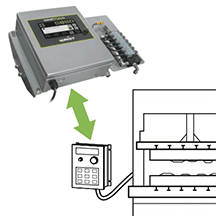
Press control interface
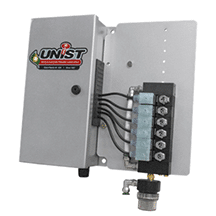
Remote valve enclosure
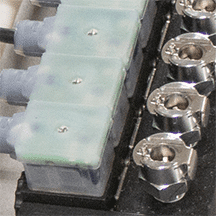
Flow monitoring
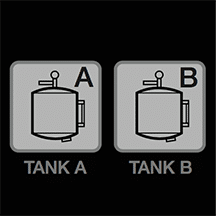
Dual fluid supply
Related Videos

Rebuilding MV Pumps
Learn how to rebuild your MV (Multi-Viscosity) pumps.
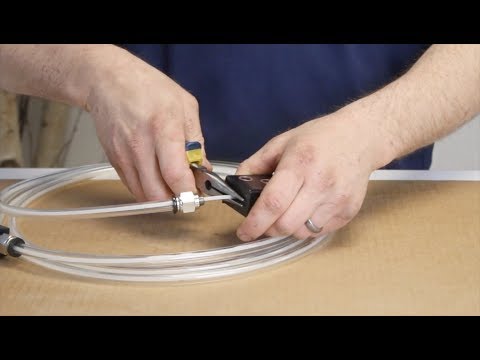
Tips & Tricks of Working with Coaxial Tubing
Learn tips for working with coaxial tubing.
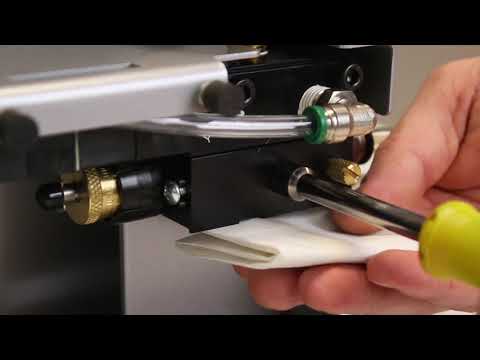
Priming A Pump-Based MQL System
In this how-to video, the procedure for priming a pump-based MQL systems is outlined

Working With The Redesigned Capillary Splicer
Learn how to replace nozzles, shorten or replace co-axial hose or retrofit your system to use the improved capillary splicer design.

Testimonial Video - Sigma Machine
Tia Stevenson from Sigma Machine talks about the Quantum™ and Coolube® lubricants.

MQL Minute #9
In this MQL Minute, John and Larry discuss Unist MQL systems with multiple outputs.

MQL Minute #7
Unist multi-viscosity (MV) pumps are discussed in this MQL Minute.
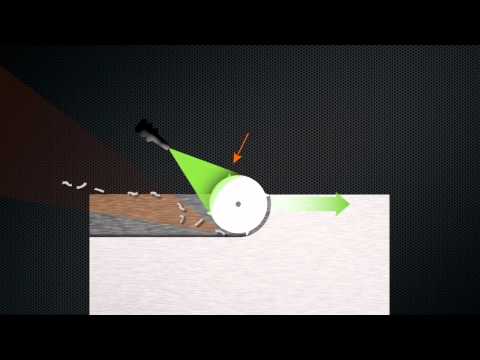
MQL Minute #6
Learn how to best position your nozzles for milling operations in this MQL Minute.
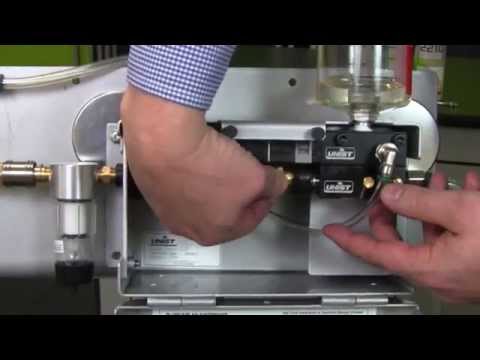
Setting Up Your Coolubricator System
Learn how to do initial setup on a Coolubricator™ system.

MQL Minute #4
In this MQL Minute, John and Larry discuss the differences between Unist Coolubricator™ and Serv-O-Spray™ systems
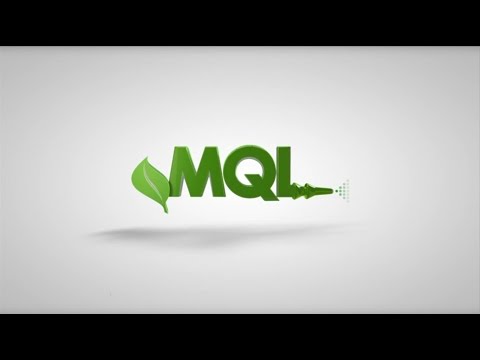
What is MQL?
An introduction to Minimum Quantity Lubrication (MQL).

MQL Minute #3
John and Larry take a look at some dry chips in the Unist shop.

MQL Minute #1
This MQL Minute provides a general overview of Unist MQL (Minimum Quantity Lubrication) systems.

Installing Coax Nozzles & Splicer Pins
This video demonstrates how to install co-axial nozzles and splicer pins in a Unist MQL system.